How BioBus Makes Fuel
What is Biodiesel and its Benefits?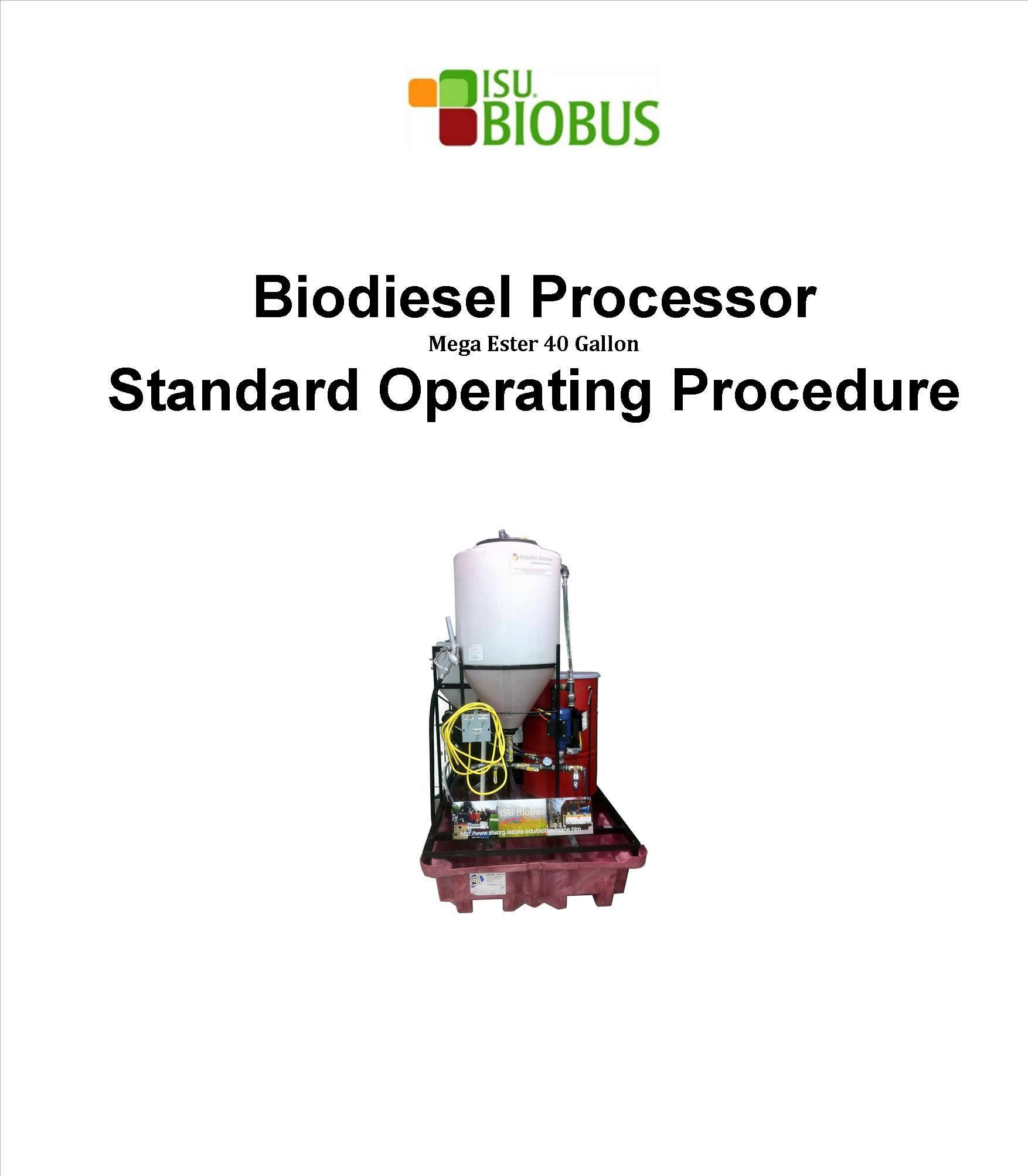
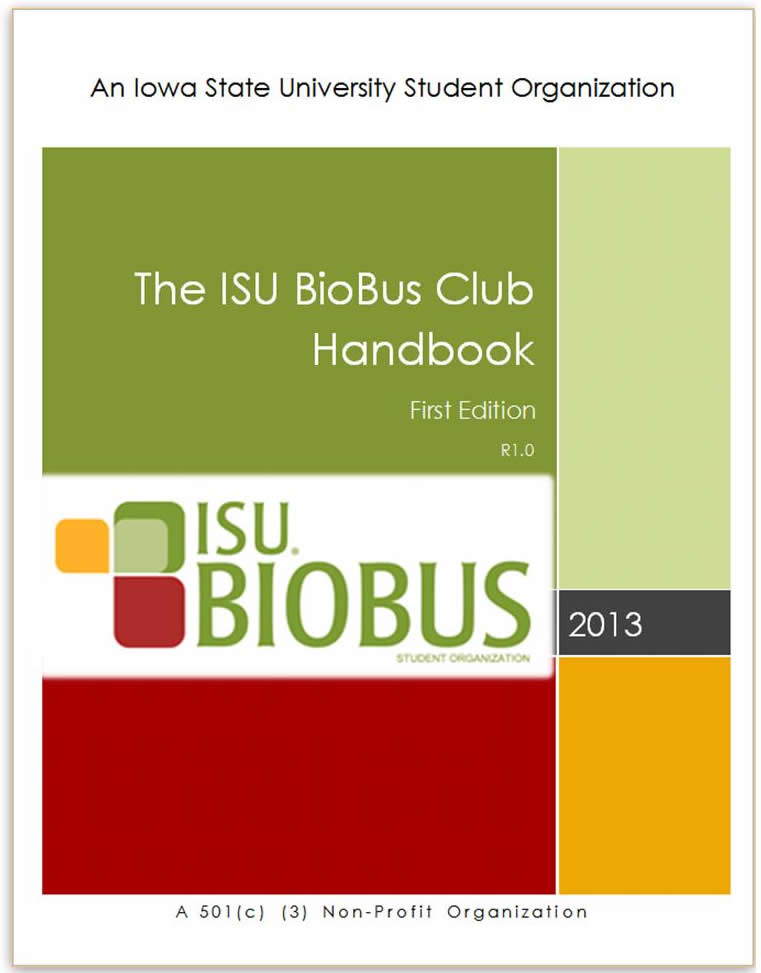
Biodiesel is one of the major biofuels that is manufactured from biological ingredients such as vegetable oil, recycled cooking oil, or animal fat. The National Biodiesel Board (NBD) defines biodiesel as - a fuel comprised of mono-alkyl esters of long chain fatty acids derived from vegetable oils or animal fats, designated B100, and meeting the requirements of ASTM D 6751. It is made by the reaction of lipids and alcohol within the present of catalyst, which is calledtrans-esterfication.This reaction produces biodiesel and also glycerin as a co-product. Biodiesel is safe to be used in diesel engines without any modification. It can be used in its pure form, B100, or blended with normal diesel fuel and create different percentage concentrations such as B20.
Using biodiesel has lots of benefits as it is an environmental friendly energy source. Compared to normal diesel fuel, biodiesel produces reduced emissions of greenhouse gases and has positive energy balance. Biodiesel is also a renewable resource and nontoxic. For countries like United States, the production of biodiesel is important to the economy as it reduces the dependence on foreign oil. Using biodiesel reduces engine wear by increasing lubrication, improves public health, helps the environment, and provides safety benefits by virtue of lower toxicity.
Biodiesel is a non-toxic, biodegradable alternative to fossil fuels. This biofuel significantly reduces harmful emissions and can be used in virtually any diesel engine with no modifications.
Aquiring Oil
300gal Tank at UDCC and Spigot
Using our machine called the Super Sucker; BioBus collects used veggie oil from the UDCC, a few blocks from our lab. This machine is a wheeled 60 gallon tank with an air pump, fittings, and a battery. The Super Sucker also has a small spill-containment kit attached. This kit includes paper towels, extra gloves, and enough clay kitty litter to manage a small spill. After aquiring the oil we wheel it back to our lab in the BRL.
Super Sucker and Our Path From the UDCC
The Reaction
First, oil from Super sucker is pumped into the processor. The oil is circulated and heated to reduce the water content. Next, methanol and catalyst (KOH) is combined into a smaller tank before adding it into the main reaction chamber. After all the catalyst has dissolved the mixture is slowly transferred into the processor. Finally, the trans-esterfication takes place and the contents sits for 24hrs to allow the seperation of biodiesel and glycerine.
Process Diagram
Washing
After the trans-esterification process is completed, two layers of product can be seen. Biodiesel is the top layer, while a byproduct, glycerol, is settled at the bottom.The glycerol is then drained from the processor to separate it from the biodiesel. Next, the biodiesel is washed using pure water to remove excess catalyst, methanol and impurities for a clean batch of biodiesel. A water hose from the wall is attached to the nozzle of the processor tank lid. The tap is adjusted to get a very fine mist. Since water is more dense than oil it flows through the oil and washes the biodiesel. Finally, once the water and impurities are at the bottom of the tank they are drained away.
Gycerol Drop Timelaps
Transportation
Before the biodiesel is put in fuel canisters and shipped to Cyride via EH&S the fuel must be dried. To much water in the fuel can cause rust and damage to engines. The fuel is circulated and dried again just like it was before the reaction. Once the fuel has reached the right moisture content it is pumped out of the processor and into fuel canisters to be shipped to Cyride.
Fuel Canister Transfer